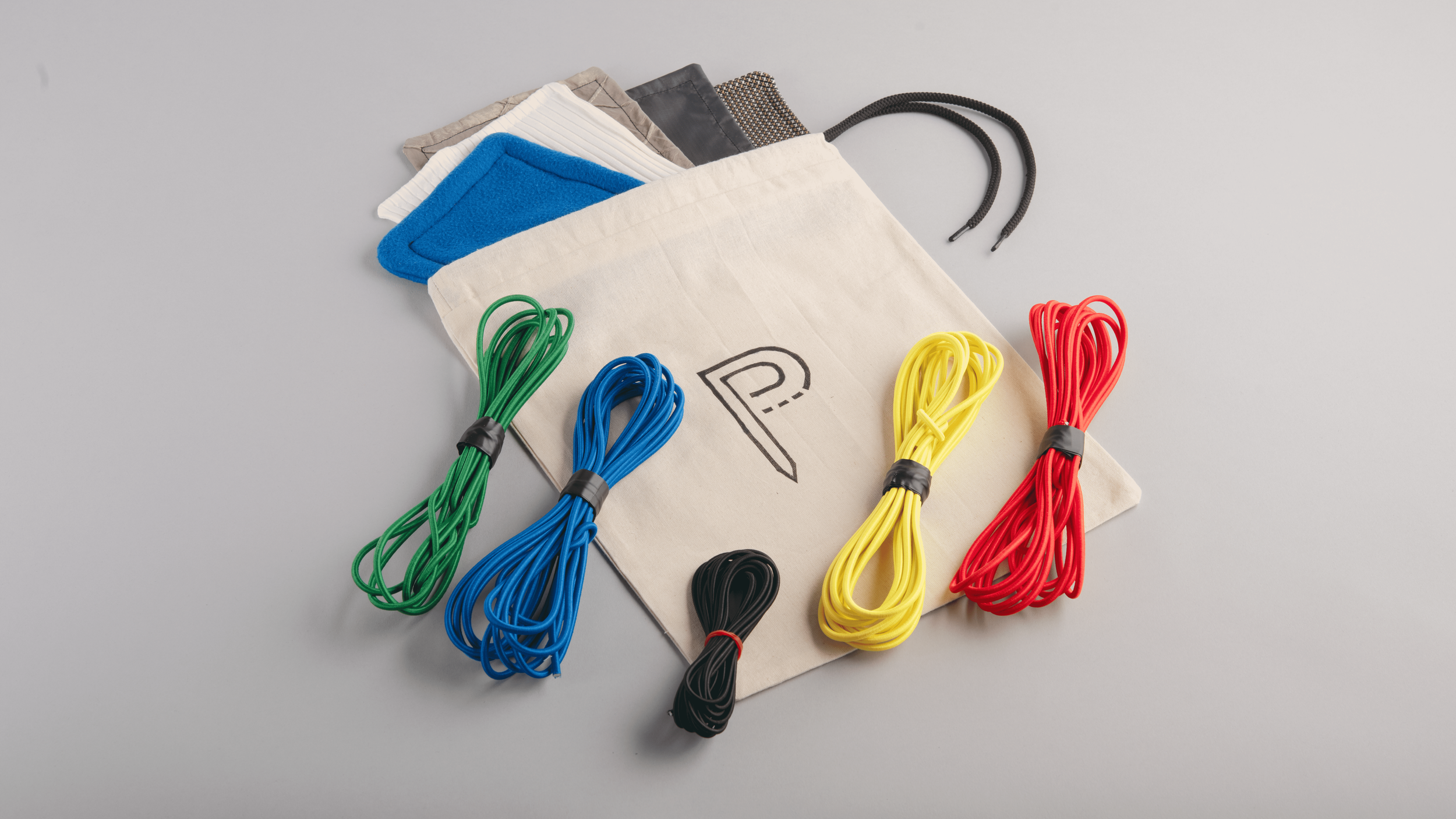
A research-driven concept investigating the future of sustainability in fashion by studying emerging practices in experimental modular, garment design.
PANELS
Sustainable Design Project
Area of Study:
Textile Waste in the Fashion Industry
Research revealed that the primary cause behind the rising levels of textile waste is the steady decline in clothing durability & quality.
- Consumer purchases have increased by 60% since the year 2000.
- Clothing durability has decreased by 36% since then.
This highlighted a growing imbalance between producers and consumers, one that results in cheaply made garments ending up in landfills with little potential for reuse or recycling.
To address this, I designed a modular clothing system that could help users co-design, customise, and repair their own clothing.
By extending the life of each garment, this empowers users to take an active role in reducing their contribution to landfill waste.
Image: Textile waste from Kantamanto Market pollutes a beach in Accra, where an estimated 15 million items of used clothing arrive weekly from the global north.
Introducing PANELS.
A product-service system offering sustainably designed modular garments, in an effort to mitigate the impacts of overconsumption on both the environment and our wardrobes.
Using modularity, the functions and appearances of multiple clothing items can be contained within one garment, effectively reducing material waste.
Designed to be a lifelong garment, this clothing concept supports users in achieving their sustainability goals by allowing them to adapt existing pieces to suit their evolving lifestyle.
- Recycled from post-consumer waste fabrics.
- Stitched by both machine and hand.
-
The concept was created by dividing the garment into sections of modular, interchangeable panels that are stitched onto a base layer, with each panel corresponding to a different part of the body.
Features like sleeves, hoods, collars and zip pockets would become interchangeable panels that are sewn on top of the base layer to give the garment a new style and look, depending on the wearer’s preference.
-
The bio-synthetic threads used to sew the garment are engineered to degrade and unravel under specific heat conditions, allowing the panels to be easily removed for repairs or replacements with zero damage to the undershirt fabric.
Damaged panels or fabric sections removed through this method can be recycled and turned into fresh set of panels for another garment, effectively reducing textile waste using this circular process.
-
The sweatshirt features an elasticated waistband discreetly positioned within its hem, providing the flexibility to adjust for changes in the user's weight.
Using tri-glide slider buckles, wearers can effortlessly tighten or loosen the waistband width, improving their comfort for the perfect fit.
-
An innovative window lacing system was developed to create detachable sleeves, meaning the garment could transform into either a T-shirt or a long-sleeve sweatshirt, depending on the user's preference.
This feature also makes the garment adjustable in size, as the pull cords embedded in the sleeves allow the length to be easily altered for a better fit.
The Future of Fashion Design
Minimal. Affordable. Inclusive.
The goal for this project was to make accessible clothing that seamlessly integrates into any wardrobe.
The minimal design served as a canvas, that could encourage others to express their individuality, using the principle of modularity to materialise the boundless possiblities available with clothing customisation.
In theory, every aspect of the garment could be altered to reflect the individual’s personal taste.
From the material and texture of the fabric, to the sleeve length and waistband of the sweatshirts, the individual can be given full autonomy to create a piece that is uniquely theirs.
Product Visuals
Swipe to see further garment details.
Garment Production
Manufacturing Process:
The garment has a base layer as a foundation, on which the modular panels for each section of the body are placed & stitched on top to complete the garment.
Synthetic heat-dissolvable threads will be used to sew these panels onto the garment using industrial sewing machines.
Disassembly Process:
During disassembly, the panels are exposed to temperatures reaching up to 190 °C. This controlled heat causes the synthetic threads to degrade and unravel, allowing the panels to separate from the garment without damaging the base fabric.
Less Waste, More Impact.
By intergrating modular design into traditional methods of garment construction, significant reductions in both material and resource depletion could be achieved with the PANELS concept.
The product’s adaptable structure supports a closed-loop system, enabling garment-to-garment recycling and significantly cutting down textile waste.
Opportunities for circular material flows can also be further supported with the development of mono material and regenerative plant-based fabrics that could be used for the production of new panels for the garment.
Product-App Intergration
An accompanying PANELS app was developed to connect customers directly to the garment’s supply chain, allowing them to access clothing alteration services through booking and order delivery.
Additionally, users can connect with other community members interested in sustainability and explore marketplaces for inspiration for their next clothing alteration project.
I would love to share more about my design process with you! If you have any questions, need more information, or just want to chat about my work, feel free to connect.
Let's start a conversation.